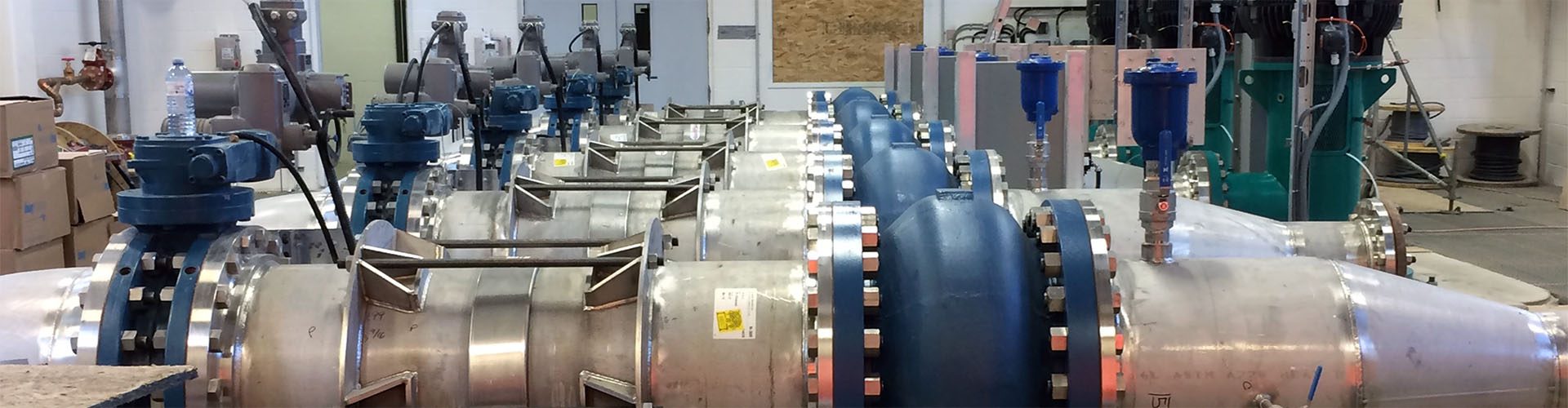
Hydraulic/Water plant commissioning process comprises the integrated application of a set of engineering techniques and procedures to check, inspect and test every component of a water plant. This is from individual functions, such as instruments and equipment, up to complex items such as modules, subsystems and systems. Commissioning activities, in the broader sense, cover all activities from end phases of the construction and assembly, until the final handover.
Why is this necessary?
During the engineering design, there are so many aspects that cannot be visualised sitting in an office. Results in at the construction phase many surprises show up. Sometimes, plant construction material and equipment such as valves, piping, pipe fittings and instruments, for example, may not be exactly according to the specifications raised in the engineering phase. This is either due to either human error, unsuitability or non-availability of a particular type of material or item considering the schedule or details of the plant commissioning. Some modifications have to be done to meet deadlines for plant commissioning.
In short, everything is not as ideal as it should be and alternative solutions are required. Also, there may be errors and changes during the engineering design itself, and these need to be rectified during the construction phase and consequently the completion and commissioning. Based on the above-mentioned, the need of commissioning drawings and documents arises. As the name suggests the drawings reflect what has been actually commissioned at the plant.
This allows the facility manager to feel comfortable that all documents are corrected and back-checked against the mark-ups by the engineering team.
Supported Standards
Expand list
AS/NZS 3666.1:2011 | Air-handling and water systems of buildings |